BoatNews.com

Steel boats: the advantages and disadvantages of this hull material
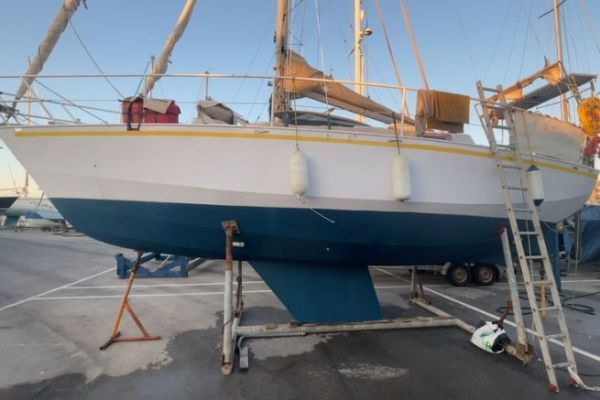
Steel boats are the talk of the pontoons. Bernard Moitessier and other sailors of the time all chose this material for various reasons. There are also a good number of launches still built in steel. But why are they still relevant today? What are the advantages and disadvantages of this material?

Why choose a steel boat?
After reading a book by Bernard Moitessier and other ocean adventurers, many will choose a steel boat. The steel boat is historically the travel boat that can brave all conditions, including extreme latitudes. Choosing a steel boat in the 21st century can also be a guarantee of safety in the event of a collision with a UFO . But what are the real advantages and disadvantages of these hulls?
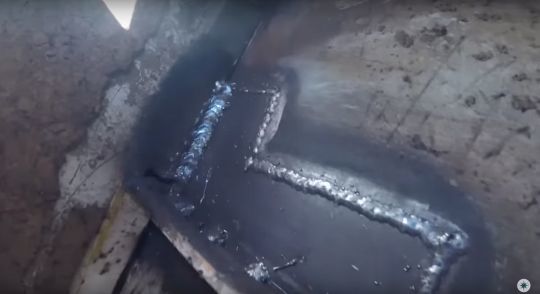
The advantages of steel boats
Uncompromising strength: a well-built steel boat can withstand all weather conditions and even collisions. It will often come out with a few dents, but should remain watertight.
Durability: well-treated steel is a material that lasts over time. Almost all large vessels (ferries, container ships, merchant ships, etc.) are made of steel , and many are over 50 years old. What's more, steel is easy to recycle.
Cheap and "easy" repairs: if there's damage , or even holes, steel boats can be repaired easily. All you have to do is cut and re-weld, and a good boilermaker will be able to do it for you. And if you're good with your soldering poster, you can also do it yourself.
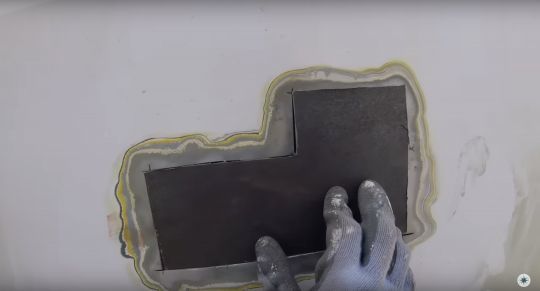
It's easy to do-it-yourself: need to add a platform to your ship? Consider welding it on. Just try to keep it elegant and sleek!
Cost: you can find bargains and inexpensive boats. However, this advantage can quickly turn into a disadvantage if the boat is in poor condition. A steel boat in poor condition can be very labor-intensive, and you'll need to be prepared to spend a few months or years in the yard before you're ready to sail .
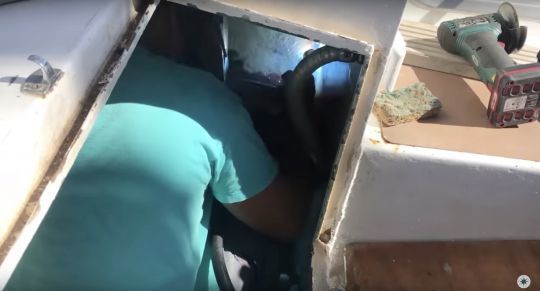
Disadvantages of steel boats
Strong, but heavy: steel is much heavier than other materials. For example, a 9-meter boat can weigh up to 7 tons, while the same boat made of fiber will weigh no more than 4 tons. This means heavy displacement and a different way of sailing. The rest of the boat will have to be sized accordingly: sails, rigging, ropes...
Corrosion: this is the biggest drawback. A steel boat is bound to rust, sooner or later. As the sea is an aggressive environment, boats need to be closely monitored. You need to be able to take apart every nook and cranny of the boat to make sure there's no rust. Generally speaking, the exterior of the boat is well protected by paint, and this is not where problems appear, or at least they remain clearly visible. Corrosion is more likely to appear inside, where access is difficult: under the sink, under the shower, at the bottom of the anchor locker... If you're going to buy a steel sailboat , make sure you can explore everything.
Insulation: properly insulating your steel vessel is essential, for both hot and cold . But insulation must be "removable", so that all parts can be accessed to check for rust.
Electrolysis: rarer than on aluminum boats, electrolysis also exists on steel boats. To avoid seeing your boat turn into a battery , you'll need to keep an eye on the condition of the anodes, and change them when the time comes. You'll also need to keep an eye on your electrical installation to ensure that there are no leaks inside the boat . And last but not least, you'll need to be careful not to make direct contact with any metal you put on your boat, such as an aluminum cleat or a bronze hull pass-through (in this case, prefer a plastic one).
Steel or not?
Ultimately, well-treated steel boats offer everything you'd expect from a blue water cruiser: durability and sturdiness. But all materials have their drawbacks, and you'll have to accept being heavier and less efficient, being meticulous about rust and electrolysis, and spending a few hours treating and painting corrosion starts. If you feel you can get past these drawbacks, then you might just have the chance to weld steel links with the sea.

|
| |||||||||||||||||||||||||||||||||||
Your browser is ancient! Upgrade to a different browser or install Google Chrome Frame to experience this site. ![]()
![]() STEEL YACHT CONSTRUCTION
Steel Yacht Construction
The materials used for the construction of boats are the most important quality factor. Boats that are built of a durable material and with good workmanship and accurate planning will carry blue cruise enthusiasts safely on the vast seas, where they can enrich their inner world and discover freedom and peace of mind. One of the materials used in boat building is steel... We can define steel as a metal which passed through thick roller pipes to turn it into sheet, particularly as a ferrous material. As in all industrial fields after the Industrial Revolution, the use of steel in the construction of boats has increased as well. Steel boats built by Cobra Yacht are also constructed in accordance with the principles of high quality and fine workmanship that are applied in the construction of other boats. With steel boat construction , building quite large-sized boats that sail the vast seas quickly and safely has become easier. However, in earlier times boats built of steel were cargo boats and the use of steel in recreational crafts is a more recent development. The biggest advantages for steel boat builders to use this material are the low cost and labour. In addition, steel boats are just as resistant to severe weather and climate conditions as wooden boats. One of the most common objects of curiosity is whether or not steel boats corrode in the sea. If steel boats are painted and sandblasted properly, this type of boats will not have any corrosion problems for many years. The fact that the osmosis problem encountered in fibre-glass boats does not occur in steel boats is a big advantage for steel boat builders. As we can see with all materials, steel boats have some advantages, but they also have some drawbacks. Plate, which is a heavy material, will slow down the boats as well as making them durable. Boats in which steel is used as the material will not be suitable for those who want to have a speedy blue voyage on the vast seas. Plate boats are strongly affected by heat and cold and therefore require professional insulation. When plate boats, considered cheaper in terms of labour and cost, are compared to fibre-glass boats, it is possible to say that fibre-glass boats are more advantageous. With emerging technology, the use of computer programs in the construction of plate boats has led to a shortening of the construction time of plate boats. Cobra Yacht combines the latest technology, quality and elegance to create their vision in their world-class plate boats. What makes steel the best material for a Moonen?
What makes a yacht a Moonen? We went behind the scenes to find out how our technical team creates the world’s finest yachts. There is much more than meets the eye on a Moonen. At Moonen we only build yachts with steel hulls. Our Technical Director Nicky van Zon shares the reasons why. Advantages of steelStepping on board a Moonen steel hull yacht is often a revelation for people familiar with fibreglass or aluminium boats. There is an immediate appreciation of comfort, safety and value.
![]() What are the trade-offs of a steel hull yacht?
![]() Pre-owned Moonen yachts are highly valued. The brokerage market knows the quality of our steel yachts and this is reflected in the price. “The quality of your steel hull build is a big factor in the value of your yacht.”Moonen’s quality stems from decades of experience, the development of dedicated craftspeople and internal manufacturing capabilities that sets us apart from other shipyards. We use steel because we know it’s the right choice for our customers. ![]() If you are interested in a new steel Moonen yacht please contact us. A visit to our shipyard in the Netherlands will confirm the quality of our work and the dedication of our team. Share this storyStay informed. Sign up for our newsletter and stay updated with the latest news and updates. Don’t miss out on important information!
More contact information ![]() The Use of Steel in Boat Building![]() Steel is one of the most commonly used materials across construction, various industries, manufacturing, and fabrication. The lightweight yet strong characteristics of steel make it the premier material when both durability and efficiency are required. So, it only makes sense that steel has emerged as a dominating material in boat building–where performance, longevity, and safety are all top priorities. While fiberglass and wood are still commonly used in boat construction, continue reading below as we highlight the case for using steel in these vessels. Incomparable DurabilityOne of the most compelling reasons why boat builders would want to use steel in the manufacturing process is because of its unmatched strength and durability. Steel has an exceptional resistance to corrosion, rust, and the typical wear-and-tear that boats will undergo. So, using steel ensures that vessels can withstand the harsh marine environment without compromising their structural integrity. This translates to longer lifespans for steel boats compared to others. Especially for ships that will be exposed to saltwater and other corrosive elements, the durability factor of steel is a game-changer for sailors and the manufacturers themselves. Steel provides a strong and robust foundation that allows for the construction of large ships with complex designs. Its strength means that boat builders can create hulls that are resilient and capable of enduring the challenges that are encountered on the open waters–and it’s even fire resistant should any catastrophes occur on board. Commercial or industrial boats that need to carry heavy loads and endure extreme weather conditions over long distances will like the peace of mind that a steel ship provides. But, recreational boaters will also like the strength and stability that steel provides to their crafts. Design VersatilityBecause of the strength and malleable nature of steel, there are countless design possibilities for boat building with steel. From sleek, ultra-luxury yachts to heavy-duty industrial ships, steel can be molded into various shapes and sizes, catering to a wide range of uses and preferences. So, aside from the functionality of using steel in boat construction, it also allows builders to create aesthetically pleasing vessels without detracting from the integrity of the ship. Less MaintenanceBecause steel is corrosion-resistant and doesn’t typically undergo the same wear and tear as other types of building materials, it minimizes the need for extensive maintenance. Of course, a steel ship will still require essential routine maintenance. But, the frequency and severity of the upkeep are generally lower than what you’ll find with wooden or plexiglass boats. All in all, this results in cost savings and less downtime for the ship owners. More Eco-FriendlyThere are also positive environmental implications to using steel for boat building. Since steel is a recyclable material, many boat manufacturers can utilize recycled steel to reduce their carbon footprint and impact of manufacturing. Plus, the durability and longevity of steel vessels make them have longer lifespans, which leads to reduced waste in the marine industry. RELATED INSIGHTS![]() The Future of Steel Pipe Manufacturing: Trends and Innovations![]() Why Stainless Steel Pipe is the Preferred Choice for High-Pressure Environments![]() Understanding API 5L Pipe Specifications: A Comprehensive Guide for Industry Professionals![]() Navigating ASTM Standards for Steel Tubes and Pipes: A Procurement Manager’s Guide![]() The Ultimate Guide to Selecting the Perfect Steel Pipe for Your Industrial Project![]() Maximizing Efficiency: The Versatile Applications of Steel Pipes in Industrial Projects![]() How Federal Steel’s Custom Steel Solutions Meet Industry-Specific Needs![]() ![]() The Comprehensive Guide to Choosing the Right Steel Pipe for Your Project![]() The Benefits of Using Carbon Steel Pipe![]() Exploring the World of Specialty Pipe and Tube: A Comprehensive Guide![]() New Construction Yachts – Materials for Building Boats29 February 2016 MATERIALS GUIDE FOR BOAT BUILDINGWhether you’re considering to build a new construction yacht or purchasing a pre-owned boat, you will come across the question of what’s the ideal material for building one or consider one already built. In the past century, boats have evolved from wood to composite and the naval architects and shipyards have added steel, aluminium, various plastics, and even Ferro-cement to the material list. And now each material is available in a variety of forms. As a result, many yachts employ several materials, and you will notice the possibilities are endless. As new materials were introduced, many of them in the post-war boom of the late 1940s and early 1950s, boatbuilding opinions are different. Early wisdom indicated that steel was most suitable for large yachts and fibreglass appropriate only for small boats, but these were only early opinions. Adequate material selection, whether you’re building a single new construction yacht or a series of them, is critical to success. Among the many factors to consider, the most important are weight, strength and corrosion resistance. Secondary to these are the size and shape of the hull, the intended use of the vessel, and her cruising area(s). There are also differences in material and labour costs which, in the end, can represent a substantial percentage of a fully equipped and finished yacht. Each of these materials has pros and cons, so, it is not surprising to see naval architects, designers and shipyards pick and choose to create custom yachts from a mix of materials. In the 50 to 200-foot range, the following common materials are successfully used nowadays: Wood is the traditional boat building material used for hull and spar construction. It is buoyant, widely available and easily worked. It is a popular material for small boats (of e.g. 6-metre (20 ft) length; such as dinghies and sailboats). Its abrasion resistance varies according to the hardness and density of the wood and it can deteriorate if freshwater or marine organisms are allowed to penetrate the wood . Woods such as Teak, have natural chemicals which prevent rot. Wood can be worked as solid planks or plywood. Today, many boats are cold-moulded using wood strips and resin. Wood offers thermal, acoustic, and aesthetic advantages that other materials, particularly metals, find tough to match. Saturating the wood in resin reduces maintenance issues, but does not eliminate them. Steel is either used in sheet or alternatively, plate [14] for all-metal hulls or for isolated structural members. It is strong, but heavy (despite the fact that the thickness of the hull can be less). It is generally about 30% heavier than aluminium and somewhat heavier than fibreglass. This material rusts unless protected from water (this is usually done by means of a covering of special paint). Modern steel components are welded or bolted together. Steel is strong, even in light gauges, and can be repaired at even the most rudimentary facilities. It is amenable to both cold and hot climates, allowing it to be shaped into compound curves and complex shapes. Susceptibility to rust is a slight disadvantage. This can be minimized with careful attention to design, construction details, and the proper application of modern coatings. Steel is frequent on Displacement and/or large new construction yachts. Aluminium , which is costlier than steel, is very light for its strength. Proper selection of marine alloys is essential; other grades will not resist in a salt environment. For yacht-grade finishes, the application of fairing compound is usually required, and the material is susceptible to corrosion if proper precautions are not taken. Aluminium is either used in sheet for all-metal hulls or for isolated structural members. Many sailing spars are frequently made of aluminium after 1960. The material requires special manufacturing techniques, construction tools and construction skills. It is the lightest material for building large new construction yachts requiring performance (being 15-20% lighter than fiberglass and 30% lighter than steel). Aluminium is very expensive in most countries. While it is easy to cut, aluminium is difficult to weld, and also requires heat treatments such as precipitation strengthening for most applications. Corrosion is also a slight concern with aluminium , particularly below the waterline. FIBERGLASS (Glass-Reinforced Plastic or GRP or FRP)The most popular material and typically used for production boats because of its ability to reuse a female mould as the foundation for the shape of the boat. The resulting structure is strong in tension but needs to be either laid up with many heavy layers of resin-saturated fiberglass or reinforced with wood or foam in order to provide stiffness. GRP hulls are largely free of corrosion though not normally fireproof. These can be solid fiberglass or of the sandwich (cored) type, in which a core of balsa, foam or similar material is applied after the outer layer of fibreglass is laid to the mould, but before the inner skin is laid. This is similar to the next material, composite, but is not usually classified as composite, since the core material, in this case, does not provide much additional strength. It does, however, increase stiffness, which means that less resin and fiberglass cloth can be used in order to save weight. Most fibreglass new construction yachts are currently made in an open mould, with fibreglass and resin applied by hand (hand-lay-up method). Some boats are now constructed by vacuum infusion where the fibres are laid out and resin is pulled into the mould by atmospheric pressure. This can produce stronger parts with more glass and less resin but requires special materials and more technical knowledge. Older fiberglass boats before 1990 were often not constructed in controlled temperature buildings leading to the widespread problem of fibreglass pox, where seawater seeped through small holes and caused delamination, also called “Osmosis”. Sometimes the problem was caused by atmospheric moisture being trapped in the layup during construction in humid weather. Not only has this problem been now resolved by most yards but fiberglass yachts are now covered by a high-quality Gelcoat layer. COMPOSITE MATERIALSWhile GRP, wood, and even concrete hulls are technically made of composite materials, the term ‘composite’ is often used for plastics reinforced with fibers other than (or in addition to) glass. Composite types include sheathed-strip, which uses (usually) a single layer of strips laid up parallel to the sheer line. The composite materials are then applied to the mould in the form of a thermosetting plastic (usually an epoxy, polyester, or vinyl ester) and some kind of fiber cloth (fiberglass, kevlar, dynel, carbon fiber, etc.), hence the finished hull is a ‘composite’ of fiber and resin. These methods often give strength-to-weight ratios approaching that of aluminium, while requiring less specialized tools and skills. Composites are perhaps better suited to production new construction yachts rather than custom ones. Advantages include the ability to mix and match a plethora of resin and reinforcement choices to meet strength, weight, and dimensional requirements. Corrosion concerns are generally nil, but there are special concerns with electrically conductive carbon graphite reinforcements that should not be ignored. At Allied Yachting, if you’re considering to build a new construction yacht , we’ll be honoured to advise you further on the subject; please don’t hesitate to enquire with us. OUR YACHT LISTINGS:
You might also like![]() Yachting ConsultantsSale-Charter-Brokerage-Management Headquarters:34 Rue Caffarelli 06000 Nice, France Front Office:Boulevard de La Croisette – Port Canto 06400 Cannes, France T.: +33 493 43 82 83 Email: [email protected] Website: www.alliedyachting.com ![]()
![]() Steel for Sail and Power![]() S teel ships are the backbone of world trade, and navies around the world maintain their allegiance to the metal. Like-minded builders of smaller commercial fishing boats, tugs and barges also favor the iron/carbon amalgam. So why do we see so few recreational power and sailing vessels being built from what’s arguably the strongest and one of the least expensive boatbuilding materials? Before attempting to answer, it makes sense to take a close look at what steel has to offer. Riveted iron was the first step in a ship building renaissance, a trend that gave white oak and spruce trees a bit of a reprieve. Eventually, carbon was added to iron increasing its tensile strength and stiffness. At about the same time, welding expedited the building process and steel plate was cut and shaped using highly directable flame heat from oxyacetylene torches. Today, steel can also be cut with laser, plasma, waterjet, and saw blade technology. Metal workers bend hull plate over steel frames, tack weld the plate in place and eventually carefully fuse all the seams together. ![]() Stick welding became a highly prized craft essential to how frames were tacked in place and plate-to-plate seams were joined. At the heart of the process is the welder’s electrical transformer, a tool that turns AC current into lower voltage higher amperage DC current with the capacity to melt metal. Its lower voltage dissipates the shock hazard. Electrical welding harnesses an intentional short circuit. The positive and negative leads meet at the point where the welding rod touches the grounded plate. A key factor in welding involves smoothly working the rod across the seam allowing the high current to momentarily turn both the rod tip and plate into molten metal. When the steel “weld pool” cools, the resulting joint is as strong or even stronger than the hull plate itself. Pluses and minuses Mild steel, as a material, has a long list of desirable attributes along with a couple of potential showstoppers. On the plus side, resides toughness, malleability, and isotropic strength (equal strength in all directions). The net effect of these attributes includes abrasion resistance and a structure that reacts to point loads by deforming rather than tearing. It’s also the least expensive of modern small craft building materials and is relatively easy to repair. The build process can be expedited using computer aided design (CAD), numerically controlled cutting (NC) and laser, plasma or waterjet cutters that steel suppliers use to provide pre-cut hull plating that fits together like puzzle pieces. Steel boat designer Michael Kasten has found that this service can cut building time of a 45-footer by up to 40%. ![]() Rust is the enemy of every steel boat owner. Adding carbon to iron increases the metal’s strength but also ups its tendency to oxidize. As steel begins to corrode a powdery, rufous-colored scale quickly grows into flake-like layers of rust as the material’s strength and stiffness disappear. Steel ships are designed with a specific percentage of added plate thickness to account for corrosion over the vessel’s design lifespan (usually 20 years). Small craft designers can’t afford to add the weight of thicker plate and the design process seldom incorporates such corrosion compensation. Instead, contemporary coatings, meticulous preparation and application techniques will do a very good job of holding rust at bay. ![]() Streamlining steel boat construction defies the round bilge smooth curve status quo. And one of the biggest challenges involves generating hard chine aesthetic appeal and maintaining bilateral symmetry. In short, the challenge is bending flat plate into a functional hydrodynamic shape with enough aesthetic appeal to draw a sailor’s eye. In years gone by, master craftsmen struggled to twist and cajole steel plate over round bilge frames that incorporated compound curves galore. In many cases, several hundred pounds of epoxy filler had to be pasted to the hull, troweled out and sanded smooth with “long boards” to mimic the fairness of a timber or FRP hull. Today, single chine, multi chine and radius chine designs prevail. They are designed to minimize the slab-sided look and are much easier to build than a complete round bilge boat. The FRP production boat industry has helped by following automotive trends, and adding a chine to their racers and cruisers. Fine tuning stability The design challenge also includes how the significant weight of steel is handled. When it comes to vessels less than 50 feet, weight distribution becomes an even bigger issue. For example, to lessen weight above decks and still minimize deck flex, a designer must use thinner plate, 10- or even thinner 12-gauge steel. This requires shorter spans between transverse and longitudinal support or a switch to stiffer Corten steel. Some builders even switch to aluminum above the sheer, a weight saving alternative that ups costs and adds complexity. ![]() This metal transition requires the installation of an explosion welded bi-metallic strip that’s composed of aluminum bonded to steel. It allows a fabricator to conventionally weld one side of the junction strip to the hull’s sheer and then TIG or MIG weld an aluminum superstructure to the opposite side. Welding aluminum requires an inert gas to shield the arc, and the plate is harder to weld but easier to cut. The surface can be left uncoated, it will form a self-protecting, lightly oxidized layer that abates further oxidation. The steel hull, however, must be blasted, primed and painted inside and out. And as Michael Kasten professes, “clean and grit blast the surface, apply epoxy and avoid using sprayed-in foam insulation.” ![]() The all-steel alternative can also be designed as a seaworthy vessel if careful attention is paid to weight distribution and the height of the superstructure. Payload location can also be a vital consideration. During the design process, every effort should be made to place machinery and integral tankage as low in the bilge as possible. Chain, batteries, and heavier equipment should also reside in the dry spaces below the cabin sole. If a power cruiser is to be an offshore passage maker, these vertical center of gravity considerations rule out the double-decker riverboat look and it’s also wise to avoid perching a sizable runabout and lifting crane on the top deck, aft of a heavy flybridge. A fringe benefit found aboard lower air draft power cruisers is that it places cabin space closer to the waterline where there is less effect from pitch and roll and windage is lessened. Sail and power Over the last 40 years I’ve kept track of a small but hearty 45-foot tug/work boat built by Gladding-Hearn Shipbuilding in Somerset, Mass. Dragon belonged to a friend of mine and played a central role in his marine construction business. And whether he was pushing a small crane barge, towing a load of pilings up and down Long Island Sound or when the vessel was loaded up with a sunfish, whitehall rowboat and provisions for a summer family cruise to Block Island — Dragon fit the bill. For decades Captain Jim and now his oldest son Eric have followed a regular rust abatement routine. Their anti-corrosion strategy included regular inspections of hard-to-get-at confines and never painting over rust. The grinder and wire wheel effectively abraded small spots but grit blasting to “white-metal” status was used when appropriate. Their painting preference revolved around PPG Ameron products. High on their to-do list was changing zincs and meticulously servicing the trusty old Detroit 6-71 diesel. ![]() Steel sailboats and power cruisers still hold justified appeal, but it’s important to understand what ownership entails. This is especially true for those considering a DIY build of a steel cruising boat. A good starting point is a thorough review of both Bruce Roberts and Michael Kasten’s in-depth online commentary. There’s plenty of valid detail about building metal boats, both aluminum and steel. Those with experience in welding and metal fabrication have a very significant head start and finished hulls will reflect those who learn metal work during the project and those who start out with essential fabrication skills. If you’re considering purchasing a steel cruising boat it’s essential to engage a skilled, metal boat-versed, marine surveyor. But before that develop a clear vision of what you are after. A handy way to compare vessels is through the use of parametric analysis. It’s basically, a straight forward spec comparison among two or more vessels and recognition of how the numbers relate to underway characteristics. Two hulls compared In this case I’ll compare my own well-seasoned 41-foot Ericson (18,000 pounds displacement (six-foot draft, 10’ 8” beam, 8,200 pound ballast, 750 square foot sail area) with a classic round bilge, steel 37-foot Zeeland Yawl, (18,000 pounds displacement 5’8” draft, 10’ beam, 5,700 pounds ballast, 550 square foot sail area). Though the two boats’ displacements are similar, the Zeeland Yawl’s working sail area is a lot less. This is likely due to a lower righting moment (ability to resist heeling). A further indicator of this diminished stability is the lower ballast/weight ratio, even though the displacement numbers are the same. The net result is a bit less ability to recover from a deep knockdown or capsize. The designer saw this and responded with a smaller sail area that induces less of a heeling moment. In real world terms this means that the E-41 would be far more efficient sailing in light air as well as more likely to avoid a knockdown, even when both boats are deeply reefed. But when it comes to sailing higher latitudes with bergy bits floating by, or fetching up on an uncharted rocky shoal, the Zeeland Yawl’s Corten steel hull wins hands down. The reason welded steel construction has dominated the maritime industry for decades yet made only a slight ripple in the realm of recreational small craft construction is multifaceted. In part it’s due to the production efficiency of molded FRP boat building, the ongoing concern over corrosion, plus the reality that most recreational craft aren’t put to the same rugged use as commercial vessels and work boats. However, for those who sail or power cruise well off the beaten path, steel hulls are still held in high regard and to rank number one when it comes to abrasion resistance and survivability in groundings, collisions, and other blunt force trauma. n Ralph Naranjo is a circumnavigator and the author of The Art of Seamanship (International Marine/Ragged Mountain Press). Yacht Surveying Steel and Alloy BoatsJune 6, 2019 by Clifford Blaylock Leave a Comment Steel is a material formed of Iron Ore and Carbon plus other elements. The elements used to give the steel producers the mechanical and chemical properties they want to achieve. Steel has been used to build ships for over 200 years now. Modern steels for shipbuilding have a higher tensile strength than the steel used for earlier ships built. They now contain Carbon 0.21% max, and small amounts of Manganese, Silicon, Phosphorus, Sulphur, and Aluminium. This gives them an ultimate tensile strength of 400 – 520 (N/mm2). The production of Steel has now become a very precise science. In Europe, the International Organization for Standardization (ISO) specifies standards for shipbuilding materials (ISO, 2011). ![]() A yacht made from steel will be very strong but it is the heaviest out of all the boat building materials. Corrosion on steel can be a continuing problem and a maintenance headache. Some very good marine coatings are available on the market these days to help protect steel. However, if the yacht knocks or scrapes into something this can get damaged. Wood, Aluminium and FRP all burn, this makes steel the only fireproof material for yacht construction. It also has good green credentials as steel can be recycled. Good strength to weight ratio, Aluminium is lighter than steel for the same strength. For example, very roughly speaking, and neglecting corrosion allowance in steel, aluminium plate should be between 1.25 and 1.5 times thicker than steel for the same strength. Aluminium, though, weighs 168 lb./cu. ft. vs steels 490 lb./cu. ft. only 34 percent of steels weight. A lightweight boat means a lower centre of gravity for better stability and sea worthiness. More speed for less power or sail area which means improved performance. Which is the main reason aluminium was used for racing yachts for many years. Which is the main reason aluminium was used for racing yachts for many years. Aluminium being a softer metal, it is easier to work into any shape required for a hull. Aluminium does not rust as the surface forms an oxide coating which protects it. It can suffer corrosion if dissimilar metals are in contact with it, or stray currents, but so can steel. It does not require added plate thickness to allow for corrosion. Aluminium is expensive but if you compare it with the weight of steel needed to build the same size yacht. With metal being bought in £’s per lb in weight, it will be nearly half the weight of the steel needed. Aluminium has good green credentials as a boat building material which can be recycled. Aluminium has a higher scrap value compared with Steel. ![]() Design and ConstructionA steel vessel is made watertight with the hull and deck plating. The steel used should be ductile enough to be shaped, but still stiff enough to withstand the forces of the sea. However, the vessel gets its strength from its structure which is made up of transverse frames, internal bulkheads, and longitudinal framing. The structure is designed to allow a certain amount of flexibility. But must be strong enough to withstand the forces imposed upon it by water pressure. Therefore, the framework is tack welded to the hull plating. This makes the hull plating into small panels which do not bend so easily. For example: A 4.75mm thick aluminium plate 250mm by 750mm will deflect by almost 1 x it’s thickness (4mm) when a pressure loading of 12PSI is applied. However, a larger panel, 400mm x 1000mm, would deflect by approximately 20mm with the same pressure applied. The vessel’s structure will have the weight and torque of the engine, fuel, freshwater and other equipment creating an opposite force to the water pressure. The rig of a sailing yacht also causes loads on the structure, with the tension of the mast’s stays and sails. The careful design of the vessel must spread the various loads over the internal structure. This must also support the hull and deck plating to prevent collapse under various loads, as above. Surveyors Test MethodsA surveyor must try to find defects on a steel or aluminium vessel without doing any destructive testing. A surveyor looks for defects by looking into every space onboard a steel or aluminium constructed craft. Getting down into the bilges and engine compartments with his torch and magnifying glass. Looking for cracks, dents, rust, broken parts, or bad construction practices, which could affect the structural integrity of the vessel. To do this difficult job he has certain test methods available to help him come to his conclusions. First are his sight and good lighting for visual inspection. A mirror with a light on a long handle is handy for reaching difficult to get at spots. I have a snake camera/video scope for this which is a camera on a bendable probe. The picture comes up on my phone through a Bluetooth connection and photographs can be taken with it. A camera is useful for taking photographs of defects which will be added to the report. A 1kg or 2-pound ball-peen hammer is an especially important piece of test equipment for steel vessels. Along with trained hearing, which becomes used to the percussion when hammering plates, frames, and other parts to check for hidden rust, on steel vessel. The sound from steel when struck with a hammer has a good ring to it. This sound gets duller on the thinner plate, through rust or light scantlings. Sometimes, on frames bits of rust will fall off and the remainder of the frame/plate can be measured with a Vernier. When pitting is seen a pit gauge can be used to measure its depth into the surface of the metal. Testing WeldsWhen a surveyor is looking for defects in a weld, the first thing will be a good visual inspection of the welds. Is there enough penetration, is there any undercut, porosity, or cracks? Also, is there enough weld and is the size of the weld big enough for the thickness of the metal. The surveyor can use a dye penetrant to help him with his visual inspection. First, the weld is cleaned with a wire brush, preferably a stainless-steel brush if on an aluminium hull. A dye penetrant is simply just sprayed on, then after a few minutes the excess is wiped off and a developer is sprayed on. The developer draws the dye out of the surface defects and shows up any cracks or porosity. Ultrasonic Thickness GaugeA steel vessel can lose some plate thickness each year. The equipment used for finding the vessels plate thickness without destructive testing these days is called Ultra-sonic thickness (UST) gauging equipment. The traditional way was to drill small holes in the hull. However, with the new ultra-sonic testers which have probes that use multiple echoes. This allows measurements to be taken through surface coatings, which means not even the paint is damaged. I have an ultra-sonic thickness meter to determine the remaining plate thickness of the hull structure. I have a Cygnus 4+ Ultrasonic thickness gauge which is compact and portable. It is a handheld instrument with a digital display and is designed for the marine environment. It can be used with a choice of ultrasonic probes to suit the material and thickness. The gauge measures material thickness using three methods; Single Echo, Echo-Echo or Multiple Echo. Echo-Echo and Multiple Echo allow measurements through surface coatings. Ultrasonic thickness surveying (UTS) is a non-destructive measurement of the local thickness of a solid object like metal. An ultrasound wave travels through the metal and reflects off the other side at a constant speed. Using the measured speed, called the celerity, and the distance travelled by the wave. The object’s thickness is then calculated by the meter. Leave a Reply Cancel replyYour email address will not be published. Required fields are marked * Save my name, email, and website in this browser for the next time I comment. ![]()
Home » What are the materials used in yacht construction? ![]() What are the materials used in yacht construction?Yacht construction involves the use of various materials, each chosen for its specific properties and suitability for different parts of the yacht. The choice of materials can impact a yacht’s performance, durability, and overall design. Here are some of the common materials used in yacht construction: Fiberglass (GRP – Glass Reinforced Plastic): Fiberglass is one of the most popular materials for yacht hulls and superstructures. It’s lightweight, durable, and relatively easy to shape, making it a cost-effective choice for many yacht builders. Aluminum : Aluminum is often used for building yacht hulls, particularly in high-performance sailing and motor yachts. It is lightweight, corrosion-resistant, and has excellent strength-to-weight ratio. Aluminum yachts are known for their speed and fuel efficiency. Steel : Steel is another material used for yacht construction, particularly for large, long-range motor yachts and expedition vessels. It offers durability, strength, and stability, making it suitable for ocean-crossing yachts. Wood : Traditional wooden boatbuilding techniques are still used in yacht construction, especially for classic and custom yachts. High-quality hardwoods such as mahogany, teak, and oak are used for both hulls and interior finishes. Wood provides a classic and elegant appearance. Composite Materials : Some yachts incorporate composite materials like carbon fiber, Kevlar, or epoxy resin. These materials are prized for their high strength-to-weight ratios and are often used in high-performance racing yachts. Foam Core : Yachts, particularly sailboats, may use foam core materials sandwiched between layers of fiberglass or other composites to create a lightweight yet rigid structure. This enhances both performance and insulation. Carbon Fiber : Carbon fiber is commonly used in the construction of masts, booms, and other rigging components due to its high strength and light weight. It’s a critical material in high-performance racing yachts. Plastic Composites : Some yachts feature plastic composites for specific parts, like swim platforms, seating, and interior components. These materials are often chosen for their resistance to moisture and ease of maintenance. Glass : Tempered glass or safety glass is used for windows, hatches, and portlights on yachts. High-quality glass provides visibility and protection from the elements. Stainless Steel and Other Metals : Stainless steel is commonly used for various hardware, fittings, and components on yachts due to its resistance to corrosion and attractive appearance. Other metals like bronze and aluminum can also be used for specific applications. The choice of materials depends on factors such as the yacht’s intended use, size, style, and budget. Many modern yachts also feature a combination of these materials to optimize performance, aesthetics, and durability. Yacht builders and designers carefully select materials to meet the specific needs and preferences of yacht owners. If you like this type of content, we recommend you to check our other blog posts about various yacht destinations around the world by clicking here ! Other Blog PostsAfloat majesty: exploring the world's largest yacht. In the world of luxury yachts, where opulence knows no bounds, one vessel stands head and shoulders above the rest—the world's largest yacht. With its.. Exploring Antarctica by Yacht: Is it Possible?Antarctica, the frozen continent at the southernmost tip of the Earth, has long fascinated adventurers, scientists, and explorers. Its extreme environment, pristine landscapes, and unique.. Exploring the World of Yachts: A Guide to Different TypesYachts, often associated with luxury, leisure, and a life of opulence on the open water, come in a fascinating array of types and sizes. Each.. The Best-Known Turkish Yacht - 'Dilbar’In the world of luxury yachting, Turkey has earned a reputation for crafting some of the most exquisite and innovative vessels afloat. Among these magnificent.. ![]() |
IMAGES
COMMENTS
Feb 8, 2024 · Steel is hard-core. It is a reliable yacht construction material that has proven itself throughout the years. Steel hull yachts have the best ability to withstand a collision. Even if they hit a floating object, the chance to keep floating without a crack in the hull is higher than the rest of the hull materials, still offering a smoother ride ...
Aug 11, 2023 · Why choose a steel boat? After reading a book by Bernard Moitessier and other ocean adventurers, many will choose a steel boat. The steel boat is historically the travel boat that can brave all conditions, including extreme latitudes. Choosing a steel boat in the 21st century can also be a guarantee of safety in the event of a collision with a ...
A steel yacht is now totally protected with modern paints, in fact many steel yacht owners think of their boats as a steel hull inside a plastic one. (The paint) The improvements of paint have meant that the traditional extra thickness of steel allowed for corrosion is no longer needed.
Steel Yacht Construction. The materials used for the construction of boats are the most important quality factor. Boats that are built of a durable material and with good workmanship and accurate planning will carry blue cruise enthusiasts safely on the vast seas, where they can enrich their inner world and discover freedom and peace of mind.
Jan 11, 2024 · Steel is easier to customise than GRP/fibreglass yachts – for example adding a swim platform extension or larger windows. Steel will last for generations – much longer than GRP/fibreglass. Dutch steel hull yachts built more than a century ago are still sailing today. Steel is recyclable.
Aug 25, 2023 · So, aside from the functionality of using steel in boat construction, it also allows builders to create aesthetically pleasing vessels without detracting from the integrity of the ship. Less Maintenance. Because steel is corrosion-resistant and doesn’t typically undergo the same wear and tear as other types of building materials, it minimizes ...
Feb 29, 2016 · The material requires special manufacturing techniques, construction tools and construction skills. It is the lightest material for building large new construction yachts requiring performance (being 15-20% lighter than fiberglass and 30% lighter than steel). Aluminium is very expensive in most countries.
Steel boat designer Michael Kasten has found that this service can cut building time of a 45-footer by up to 40%. Corrosion can be kept at bay by proper maintenance and modern coating technology. Rust is the enemy of every steel boat owner. Adding carbon to iron increases the metal’s strength but also ups its tendency to oxidize.
Wood, Aluminium and FRP all burn, this makes steel the only fireproof material for yacht construction. It also has good green credentials as steel can be recycled. Aluminium. Good strength to weight ratio, Aluminium is lighter than steel for the same strength. For example, very roughly speaking, and neglecting corrosion allowance in steel ...
Sep 19, 2023 · It is lightweight, corrosion-resistant, and has excellent strength-to-weight ratio. Aluminum yachts are known for their speed and fuel efficiency. Steel: Steel is another material used for yacht construction, particularly for large, long-range motor yachts and expedition vessels. It offers durability, strength, and stability, making it suitable ...